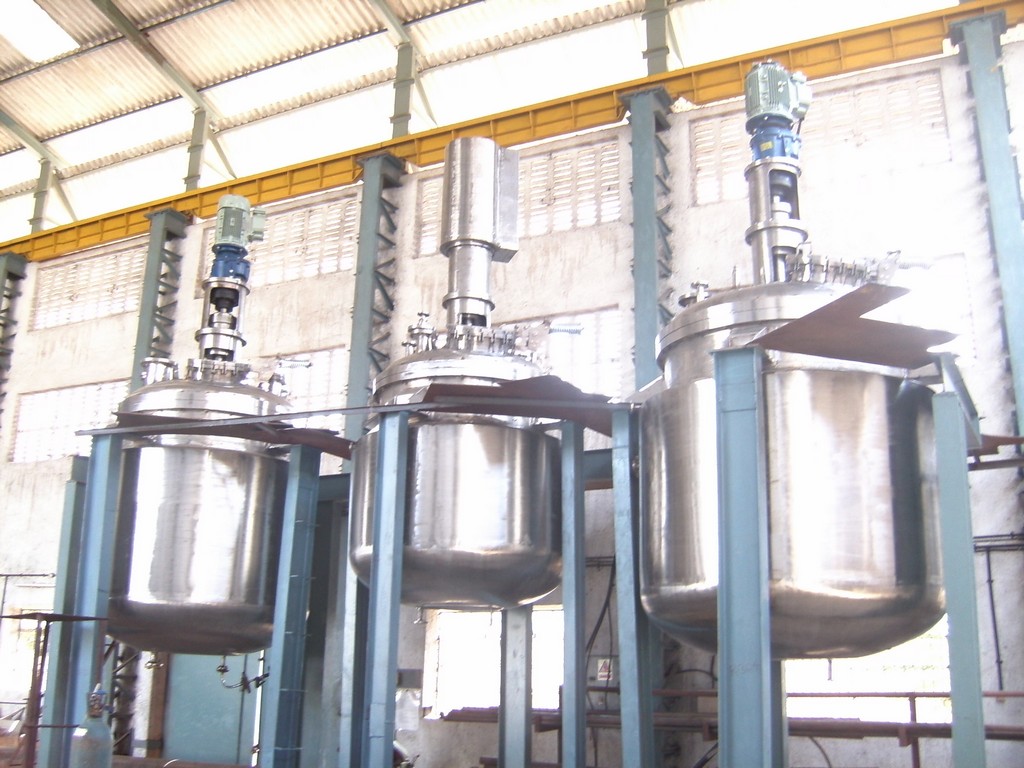
Looking for the right reactor for pharmaceutical processes? Learn how to select high-performance reactors for pharmaceutical manufacturing from a trusted SS reactor manufacturer in India.
Introduction
In pharmaceutical manufacturing, choosing the right reactor can make or break process efficiency, product quality, and regulatory compliance. From batch consistency to cleanability, every aspect of a reactor plays a role in the success of chemical and biological processes. If you’re evaluating options for reactors for pharmaceutical manufacturing, it’s important to understand the key factors that go into a reliable and compliant setup.
Why Reactor Selection Matters in Pharma
Reactors in pharmaceutical applications are responsible for handling precise and sensitive reactions. Unlike general industrial processes, pharmaceutical reactions demand strict control over temperature, pressure, and agitation, along with ultra-clean internal surfaces to prevent cross-contamination. A poorly selected reactor can result in quality deviations, downtime, or non-compliance with cGMP or FDA guidelines.
Key Factors to Consider When Choosing a Reactor
- Material of Construction (MOC)
Most pharmaceutical processes require stainless steel reactors, particularly SS 316 or SS 316L, for their superior corrosion resistance and cleanability. When selecting a reactor, ensure that the material matches the chemical compatibility needs of your formulations. A reliable SS reactor manufacturer in India will typically offer multiple MOC options including exotic alloys for special applications.
- Internal Surface Finish
Pharma-grade reactors must have a smooth, polished interior—often electro-polished to below 0.2 Ra to prevent microbial growth and allow easy cleaning. This is critical in ensuring hygiene and meeting cGMP guidelines.
- Design and Jacket Type
Choose a reactor design that matches your process: options include limpet coils, half-pipe jackets, or shell-and-tube systems for heating and cooling. The type of jacket impacts heat transfer rates, and thus process efficiency and energy consumption.
- Capacity and Scalability
Reactor sizes can range from lab-scale (a few liters) to full production-scale (up to 50,000 liters). Plan for your current and future batch requirements, especially if you’re in early-stage drug development with plans to scale up.
- Agitation and Mixing
The mixing mechanism should be tailored to the viscosity and reaction kinetics of your process. Agitator types such as anchor, turbine, or contra mixer can significantly impact uniformity and reaction time.
- Regulatory Compliance
Ensure the reactor complies with relevant standards like ASME, TEMA, and cGMP. A reputable SS reactor manufacturer in India should provide documentation, inspection reports, and support for validation during audits.
Types of Reactors Commonly Used in Pharmaceuticals
- Stainless Steel Reactors: The industry standard for general pharmaceutical reactions.
- Skid-Mounted cGMP Reactors: Fully integrated systems designed for plug-and-play installation, especially in cleanrooms.
- High-Pressure Autoclaves: Used in applications requiring elevated temperature and pressure, like synthesis of intermediates or polymers.
Manufacturing Capabilities to Look For
When evaluating a reactor manufacturer, consider the following capabilities:
- Fabrication range from 200L to 50,000L
- In-house testing and QA procedures
- Advanced machining and polishing equipment
- Customizable jacket and agitator configurations
- Comprehensive documentation and support
These attributes are commonly offered by top SS reactor manufacturers in India, who now serve both domestic and global markets.
Conclusion
Selecting the right reactor involves balancing technical specifications, compliance requirements, and future scalability. Understanding your process requirements and working with an experienced manufacturer can make all the difference in achieving consistent and high-quality pharmaceutical outputs. Whether you’re setting up a new facility or upgrading your existing plant, be sure to evaluate multiple reactors for pharmaceutical manufacturing and partner with a trusted SS reactor manufacturer in India who can deliver both performance and long-term reliability.